[VIDEO] Snacking smarter: How Darlington Snacks doubled output with automated packaging lines
By Danielle Ohl on September 26, 2023
It's an exciting time when demand for your product increases exponentially in a short period of time.
But it can also max out your current production processes and stress out your team.
Darlington Snacks needed to scale up their production to serve the increasing demands of their clients but faced challenges finding workers. With their facility located in an area dense with food manufacturing plants, they encountered tough competition when recruiting. They were scrambling to fill roles, overstressing their current employees when trying to keep up with demand.
Darlington Snacks decided to proactively meet these challenges head-on by investing in an automated snack packaging line.
Here's their story:
Business Background
Darlington Snacks is a thriving family-owned snack manufacturing and packaging facility located in Joplin, Missouri. Established in 1982, the company has grown from a small local operation to a respected national player in the snack industry. Darlington Snacks prides itself on producing high-quality, innovative, and delicious snack products that cater to a diverse range of consumer tastes.
Serving daycares, schools, and the healthcare industry, Darlington Snacks is committed to sourcing the finest ingredients for their products. They partner with local farmers and suppliers whenever possible, supporting the local economy while ensuring the freshest and highest-quality ingredients go into their snacks. This dedication to quality has earned the company a reputation for producing some of the tastiest and healthiest snacks in the nation.
Packaging Challenges
Darlington Snacks was seeing increased demand from education and healthcare organizations for snacks in single-serve containers that weren’t being handled by multiple end users, particularly during the COVID pandemic.
As a result, they faced challenges common to facilities that need to increase throughput but still package their products manually:
- Inability to scale to meet increased demand
- Unreliable labor
- Stressed out employees
- Quality and accuracy issues
Strategy & Solution
After seeing Viking Masek's VFFS Velocity packaging machine at Pack Expo in Las Vegas, Darlington Snacks began collaborating with our team of snack packaging experts to find a solution. They purchased an entire snack packaging system consisting of two bagging lines that merge into a single case packing line.
Brad Schweiss, Vice President of Manufacturing at Darlington Snacks, reports he has seen substantial improvements with the throughput and labor-related challenges they were facing.
"I’m pleased to report we’ve doubled production with about 40 percent less labor on the line." - Brad Schweiss, Vice President of Manufacturing, Darlington Snacks
Read more about Darlington Snacks' experience in their case study:
Read Darlington Snacks' full story >>Related Posts
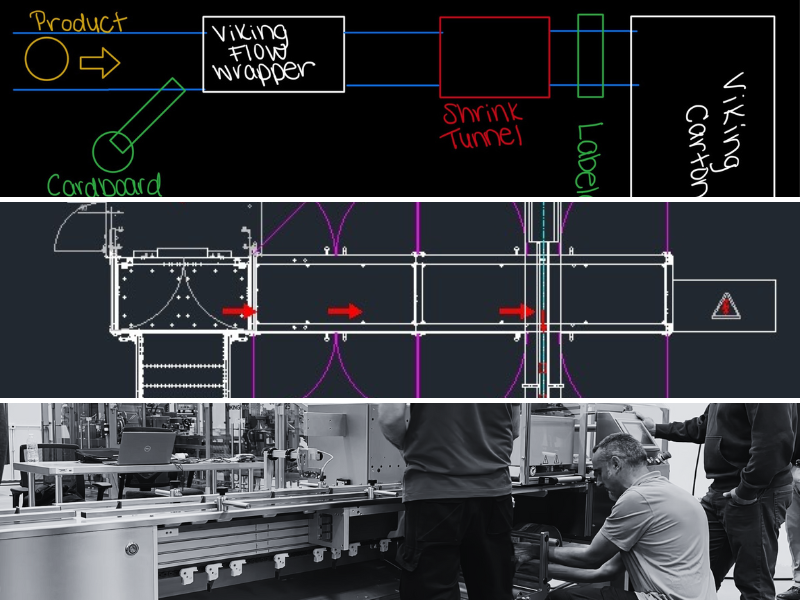
Optimizing packaging efficiency: The role of Flow Wrapping Machines in integrated systems
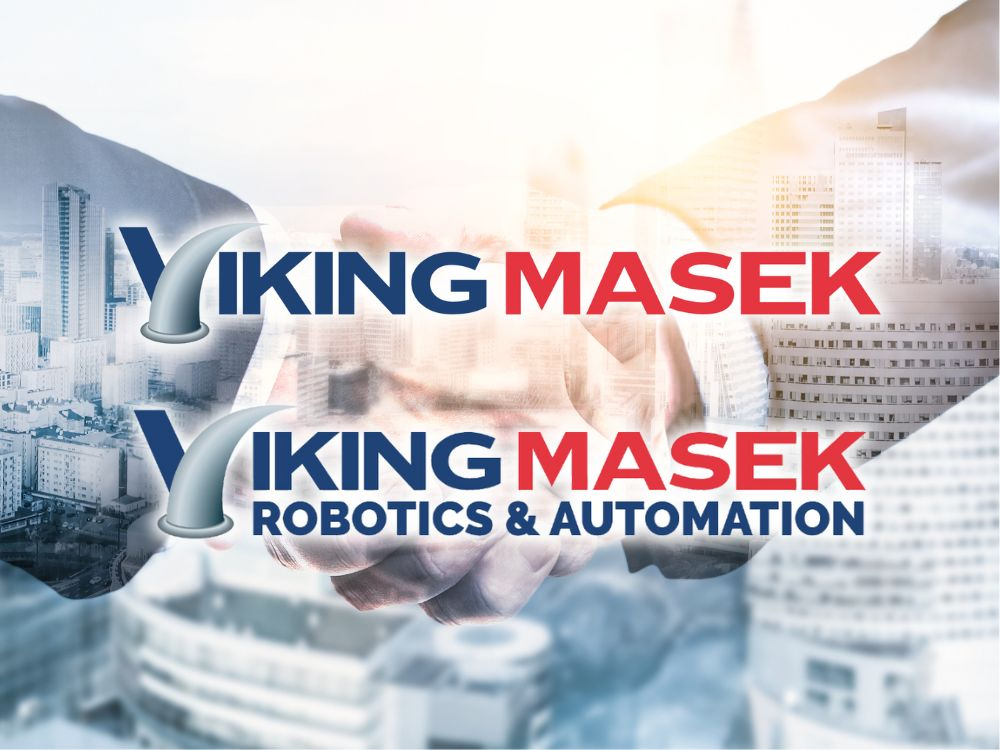
Unleashing the Power of Partnership: How Viking Masek is Revolutionizing the Packaging Industry
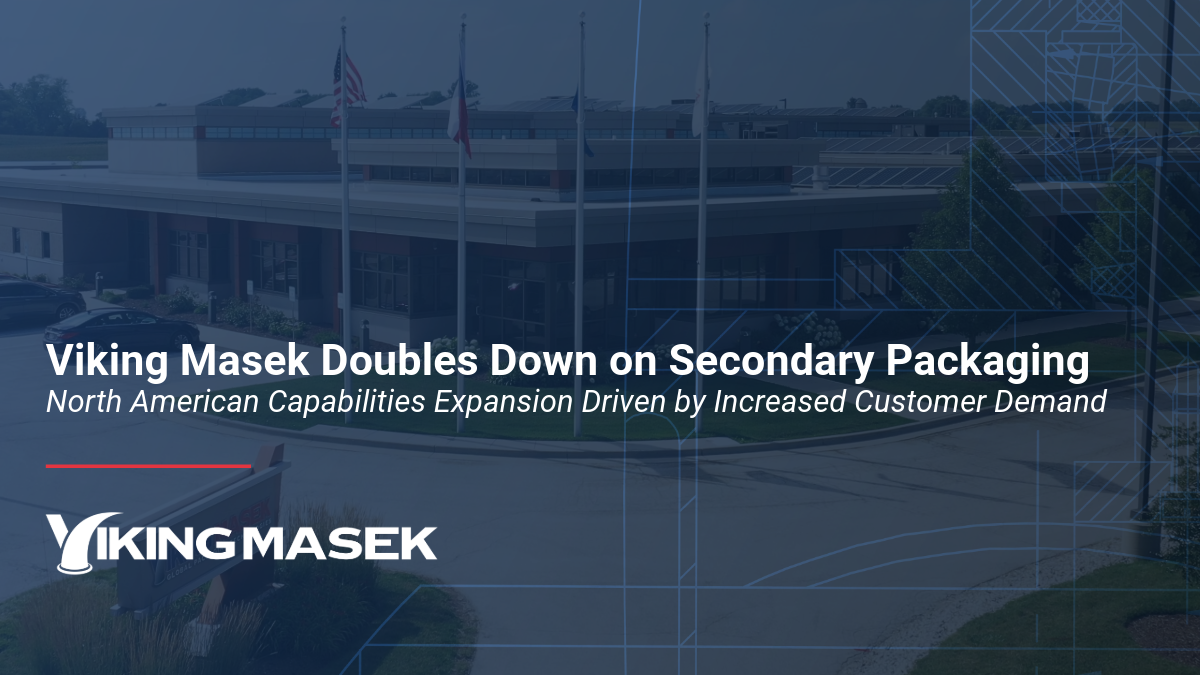