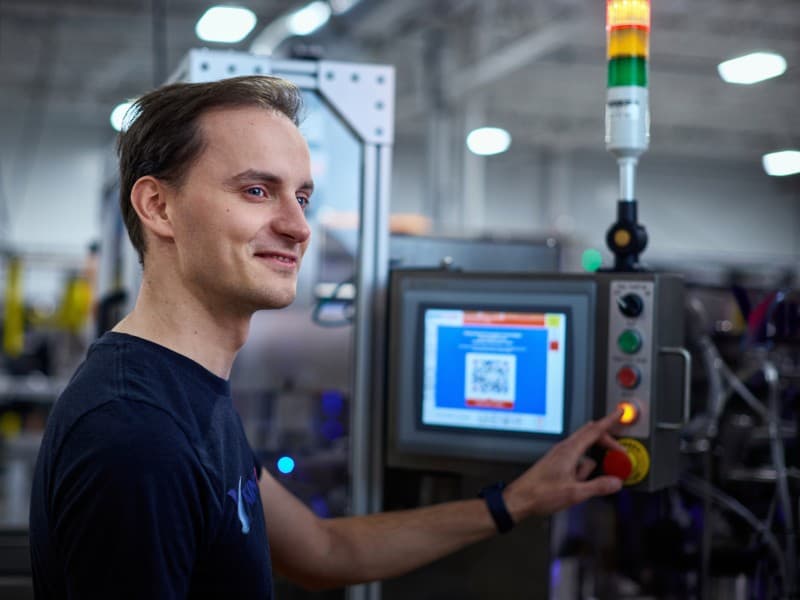
Automation Myths Vs. Facts: Why “It Won't Work For Us” Is Often Wrong
Automation misconceptions delay progress and innovation. Learn how packaging leaders overcome fear with strategic automation that works for real products.
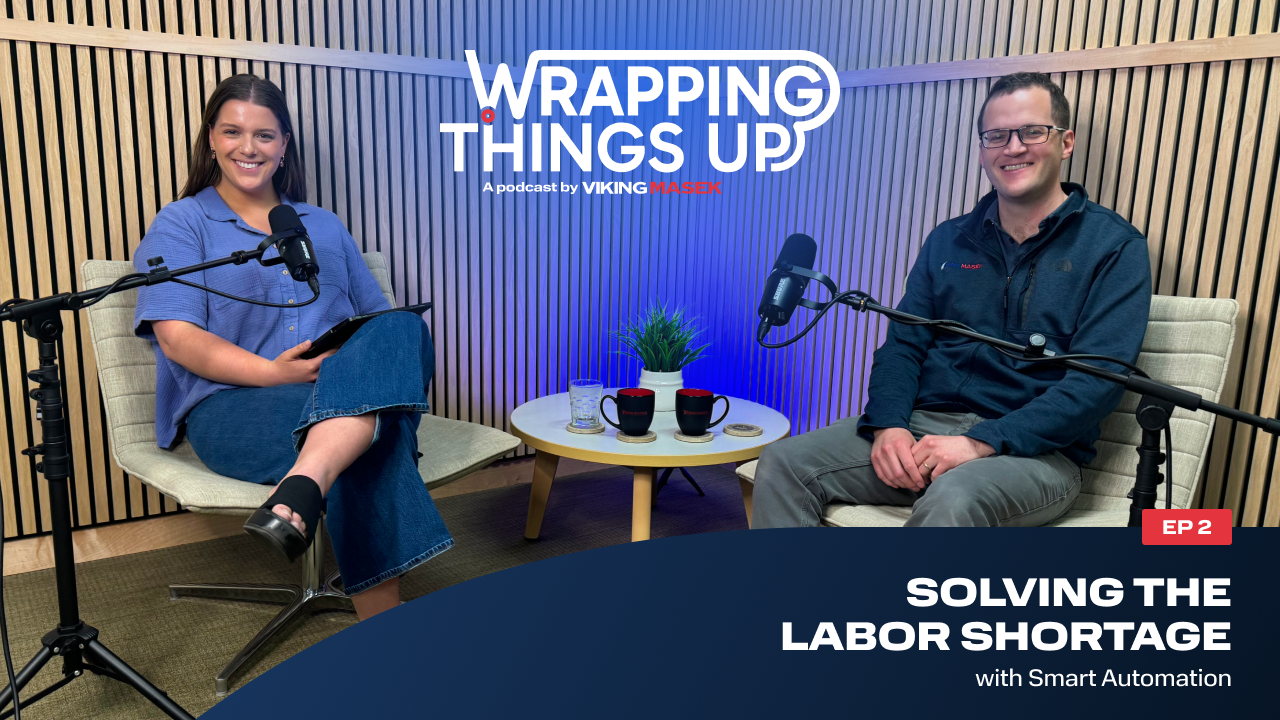
Wrapping Things Up: Automation as a Force Multiplier for the Manufacturing Labor Squeeze
Discover how automation can optimize manufacturing operations, address labor shortages, and enhance efficiency without replacing human workers.
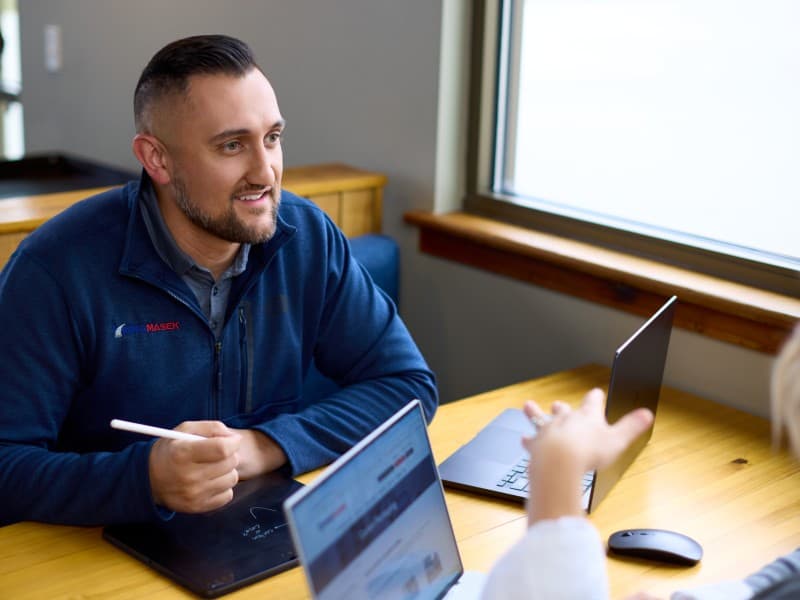
How to Choose the Right Packaging Automation Partner
Choose the best packaging automation partner with our comprehensive checklist, ensuring seamless integration & long-term success for your production floor.
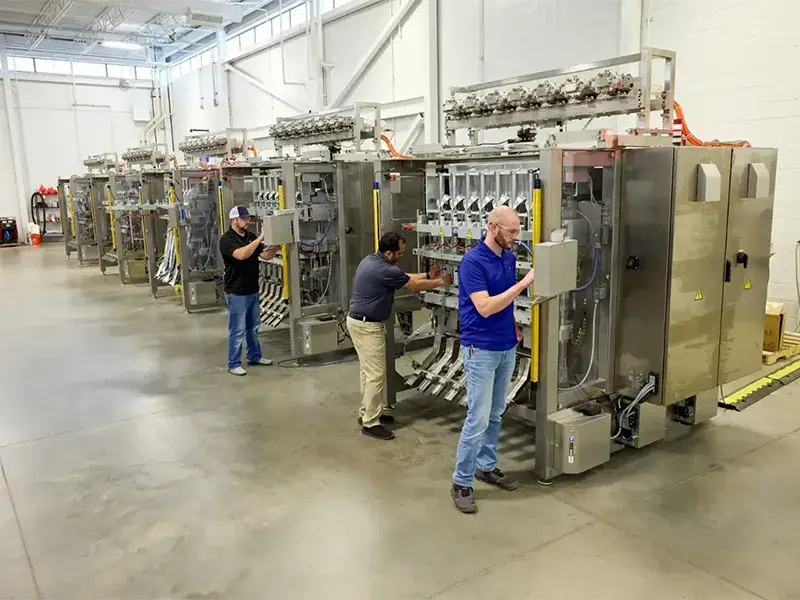
How Packaging Automation Helps Build a Stronger Workforce
Packaging automation can enhance workforce satisfaction, safety, and skill development while addressing labor challenges & boosting operational efficiency.
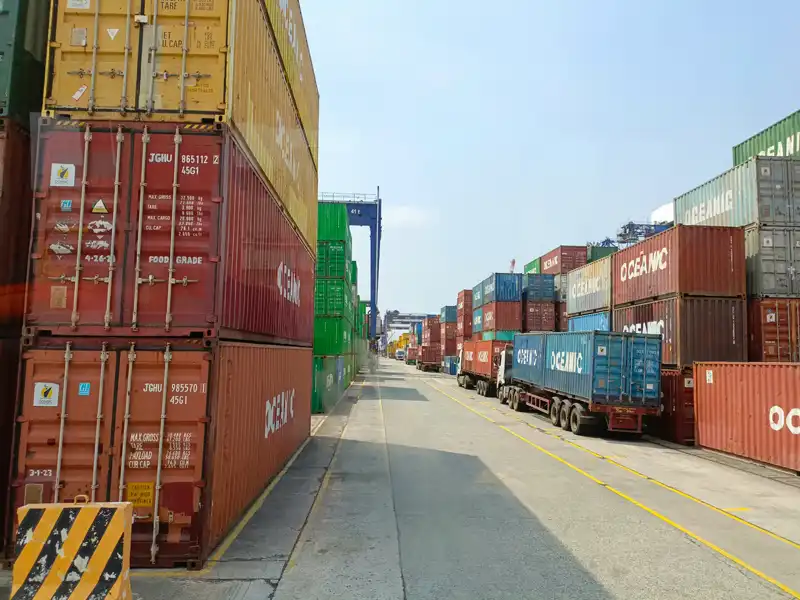
What Packaging Professionals Need to Know About Tariffs – And How to Respond Strategically
Tariffs aren’t new, but their impact on global trade and capital investment—specifically, on packaging equipment, materials, and components—decisions has become increasingly hard to ignore. From blanket tariff announcements to targeted sector-specific measures, these government-imposed fees on imported goods can disrupt even the most well-prepared supply chains.
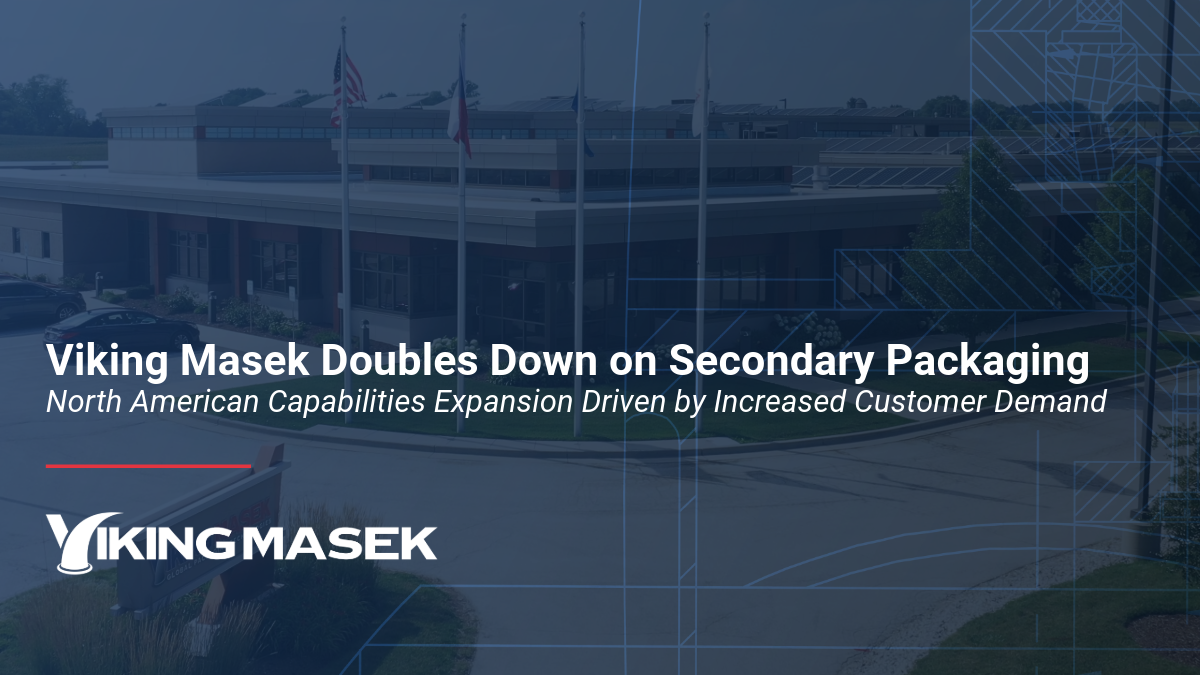
Viking Masek Doubles Down on Secondary Packaging: North American Capabilities Expansion Driven by Increased Customer Demand
As 2025 begins, Viking Masek, a global leader in simplifying the packaging equipment customer's experience, begins a new chapter. The Wisconsin-based North American operation made the decision to further bolster their secondary packaging operations to stay ahead of market demands.
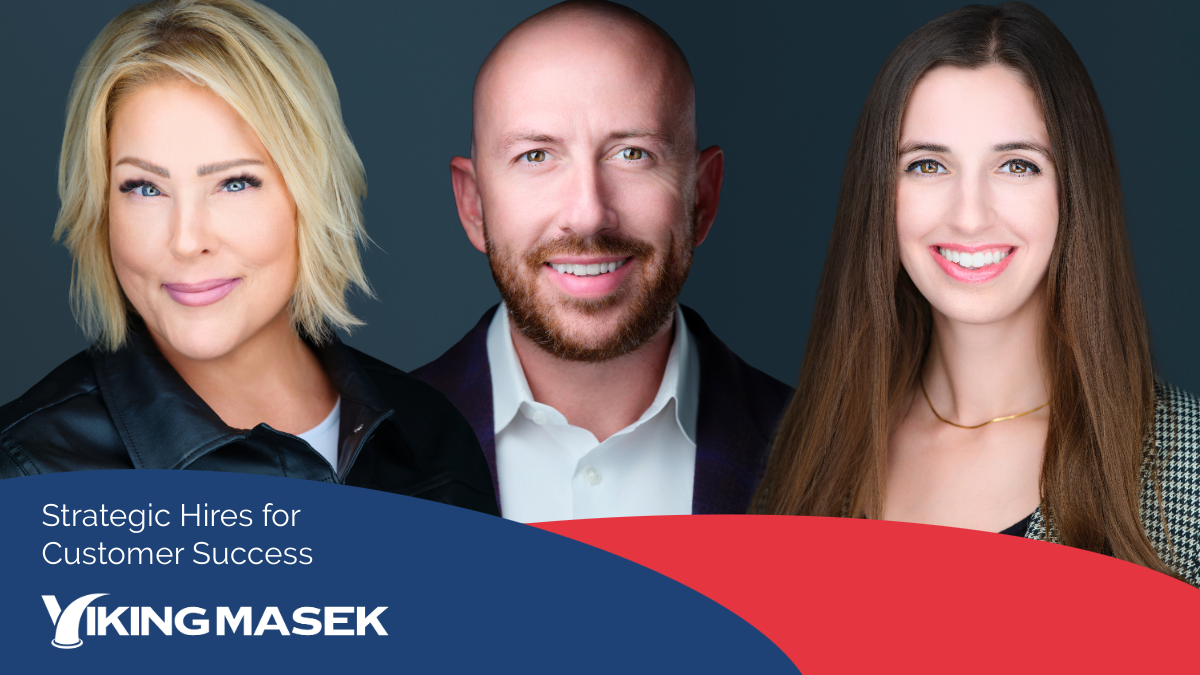
Viking Masek Invests in Customer Success with New Commercial Hires | Packaging Solutions
Discover how Viking Masek is enhancing customer success by expanding its commercial team with new hires. Learn about the company's commitment to personalized support and innovative packaging solutions.
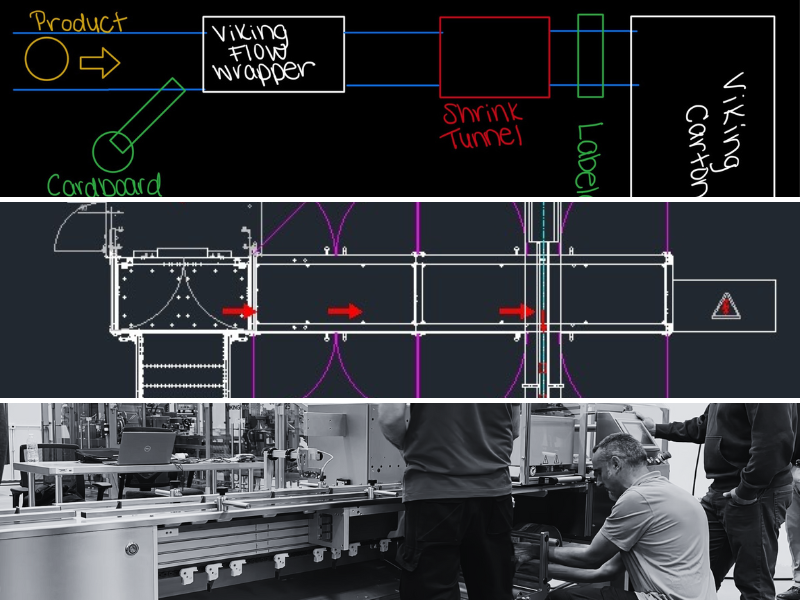
Optimizing packaging efficiency: The role of Flow Wrapping Machines in integrated systems
Discover how flow wrapping machines enhance efficiency and performance in integrated packaging systems. Learn about the benefits of these versatile machines, from improving packaging speed to maintaining product integrity, and explore their role in streamlining your packaging operations.
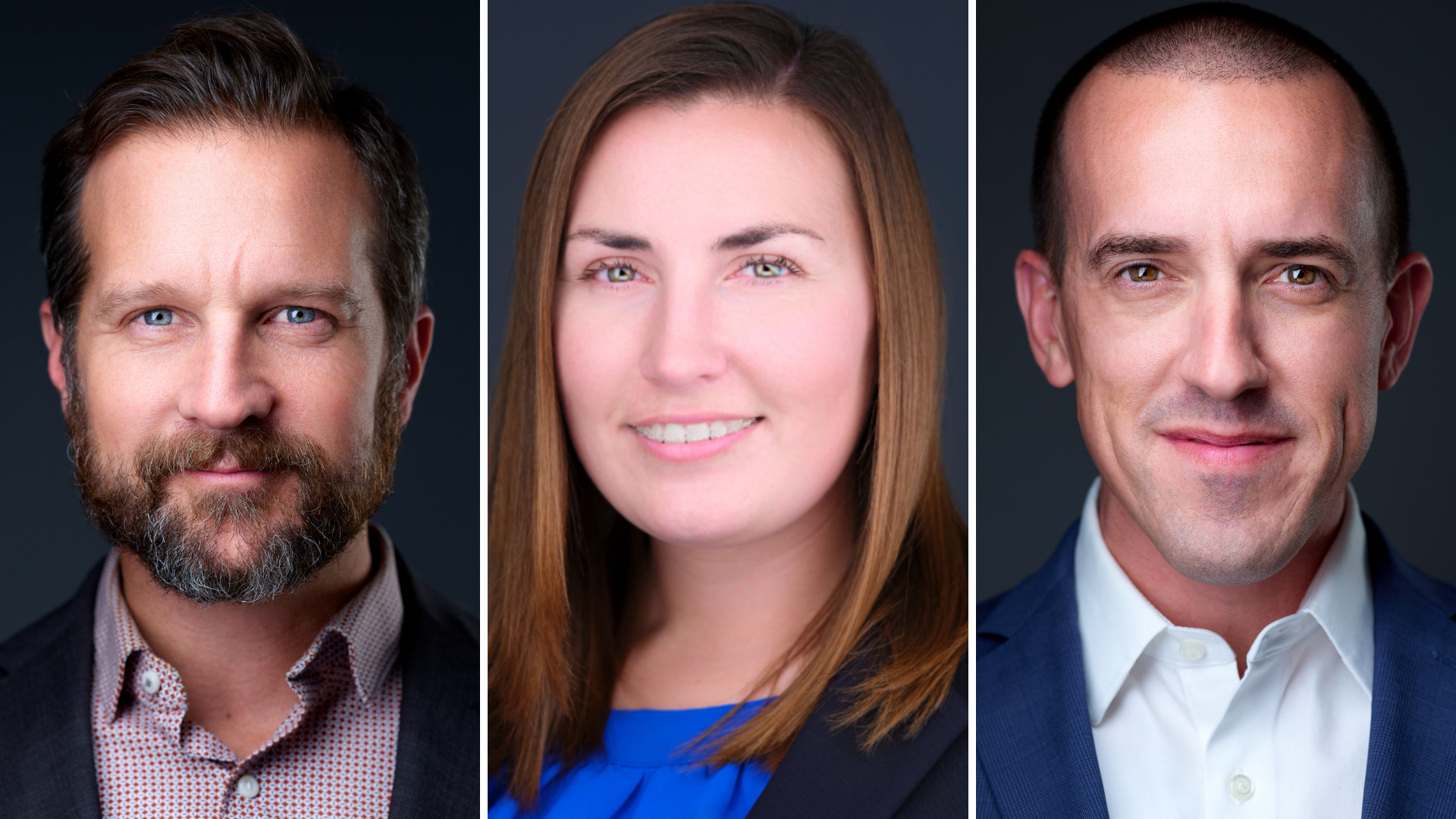
Viking Masek Enters New Era with Transition to Executive Team Leadership
Exciting times at Viking Masek as founders Robb Leonhard and Scott Miller transition to passive investors, entrusting a seasoned executive team to drive continued growth and innovation.
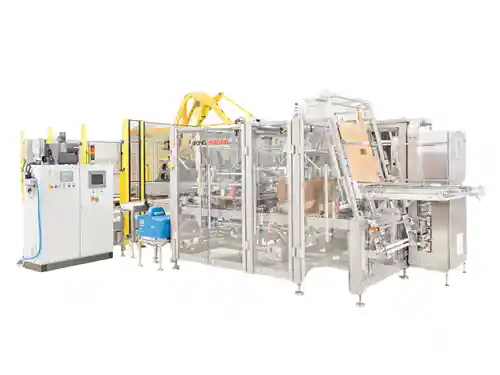
Choosing the Right Secondary Packaging Equipment for Your Needs
Finding the right secondary packaging including case packing, palletizing, cartoning, and more.