[VIDEO DEMO] How a stick pack machine works
By Scott Miller on January 7, 2021
As demand grows for convenient single-serving sticks of drink mixes and juice pops, equipment to package these items grows in popularity as well. Enter: The stick pack machine.
I'm Scott Miller, Viking Masek's VP of Product & Technology, and today I'm taking you on a video walkthrough of our most technologically advanced stick pack machine, the ST1200.
New to packaging automation? Check out our free first-time buyer's guide >>
The machine featured in the above video has 12 lanes of 37mm x 270mm stick packs and is packaging 3 oz liquid alcohol pops. A stick pack machine can be configured to match your unique specifications...from 2 to 20 lanes and stick packs of a wide range of shapes and sizes. Stick pack machines can also accommodate powders and solid items like ballpoint pens, cigars, and pre-rolled cannabis cigarettes.
Viking Masek stick pack machines are all constructed with stainless steel and clear anodized aluminum, for the purpose of sanitation and robustness of design. They come in different sizes, each capable of accommodating different film web widths:
- ST400 - 400mm web width, entry-level stick pack machine
- ST600 - 600mm web width
- ST800 - 800mm web width
- ST1200 - 1200mm web width, newest and most advanced stick pack machine
So let's dive right into our walkthrough, starting at the top of the machine:
1. Stick pack machine filler
The stick pack machine pictured in the video is fitted with a 12-lane volumetric liquid filler. There are six hoppers, each of which feeds 2 lanes.
The controls that regulate how much liquid goes into each stick pack are located on the back of the filler. Using a handle, you can adjust the stroke of the volumetric piston in the filler, giving you a larger or smaller fill accordingly.
A stick pack machine can also be fitted with an auger filler to accommodate powder products.
2. Stick pack forming
The packaging film is split into strips depending on how many lanes the machine is configured with. These strips pass over a forming assembly that guides the strips so the two vertically cut sides meet in the middle to form a long tube.
3. Vertical seal
Next, the film tubes formed in step 2 pass through the vertical seal assembly. A heated vertical seal bar (one for each lane) bonds the two sides of the strips together, creating a vertical seam on the bag. Each vertical seal bar has an individual temperature control zone, allowing for more precise temperature regulation and less temperature fluctuation. This results in stronger seals and better efficiencies with less scrap and waste.
4. Cross seal
Next, the tubes of film enter the cross seal assembly to receive their horizontal seal. This assembly uses a drawbar. Servo-driven, it moves up and down, pulling the packaging film through the machine. The distance the cross seal bar moves up and down is equal to the length of the stick, in this particular case being 270mm.
5. Product filling into stick packs
Lances connected to the liquid filler slide into the tubes that transport the liquid product to the filling area of the stick pack machine. The liquid filler pumps the appropriate volume of product into each stick right after it receives its cross seal.
If this was a powder product, an auger would measure a specific amount of product and drop it down a tube into each stick.
6. Knife cutting station
Once the stick pack receives its horizontal seal, it continues down to the knife cutting station. Each individual lane is fitted with a sharp cutting knife that separates each stick pack from the one above it.
7. Stick pack discharge
At this point, the finished stick pack is discharged from the machine. The machine pictured in the video is configured with optional individual discharge chutes that allow for more precise movement of the sticks as they leave the machine. At the end of each chute is a stop gate that rises and falls at certain intervals, aligning the sticks in each lane with downstream equipment, which in this case will be a side discharge conveyor.
8. Optional downstream equipment
The stick pack machine featured in the video will be integrated with a side discharge conveyor that will index the sticks in preparation for automatic counting. Downstream will be a counting head that will count out 12 stick packs and place them into cardboard cartons.
Additional stick pack machine features
Electrical enclosure
Located on the side of the equipment, the electrical enclosure on this stick pack machine is constructed of stainless steel and specially vented for the possibility of some liquid product coming down from above. Specifically for liquid applications, the vents give the enclosure a little extra protection.
Film carriage
Around the back of the stick pack machine is the film carriage where the roll of packaging film is loaded and threaded through the machine around various tension and guide rollers. The film carriage is completely enclosed which protects the roll of film and adds additional safety measures as this is a rather large and heavy assembly.
Film splice table
Above the roll of film, you will see a splice table, which is used to join the end of a spent roll of film to a new roll. This will automatically draw the new roll of film through the machine without having to manually re-thread it.
Pneumatic system
Stick pack machine pneumatics are incorporated into the body of the machine. Mechanical fasteners keep the door to the pneumatics closed to provide extra safety precautions.
As we look inside at the pneumatic system, you will see a mechanical drive system that controls the servo-driven cross jaws as mentioned in step 4. Viking Masek stick pack machines contain servo cross jaws for two reasons:
- Accuracy. The ability to pull and repeat each film pull exactly.
- Speed. Higher speeds are achieved; up to 45 cpm in a true production environment.
Guide for first-time stick pack machine buyers
New to the world of automated packaging equipment? Our experts have your back. Download our free first-time buyer's guide to learn how to make the best packaging automation decision for your business:
Related Posts
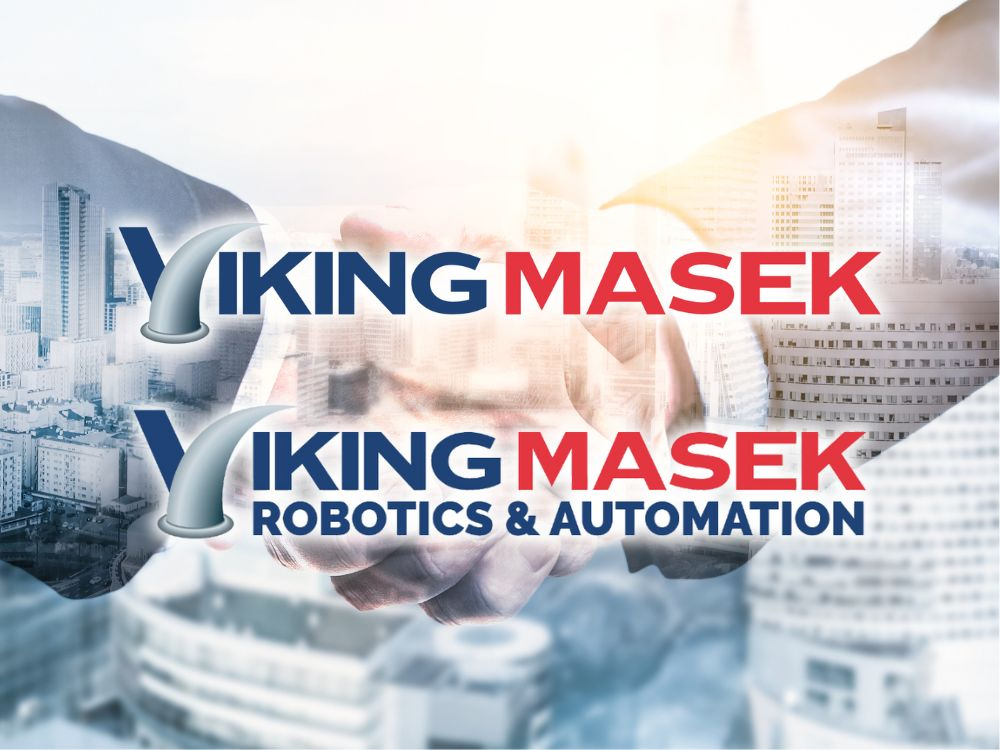
Unleashing the Power of Partnership: How Viking Masek is Revolutionizing the Packaging Industry
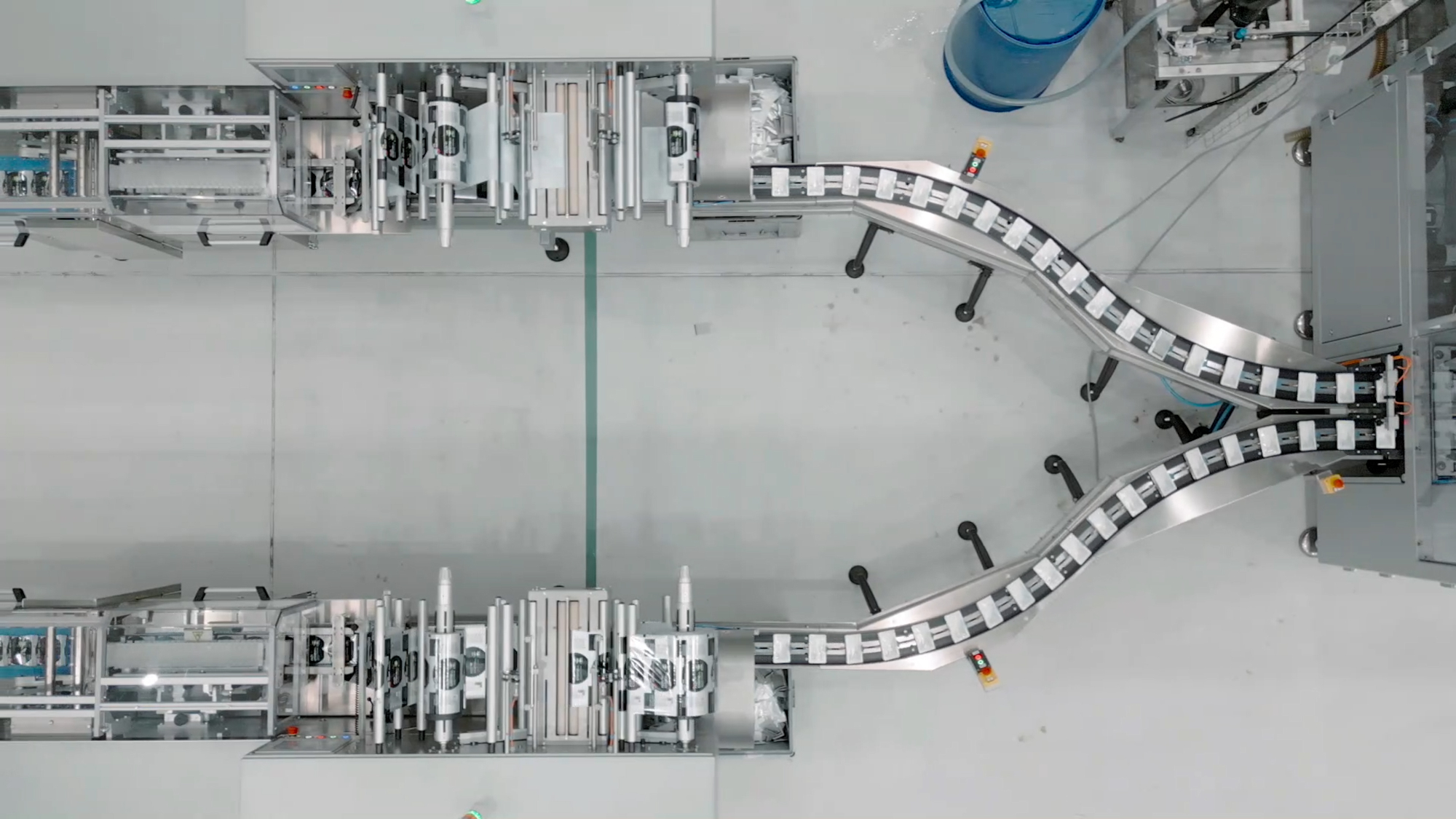
Introducing Viking Masek's advanced flow wrapping equipment
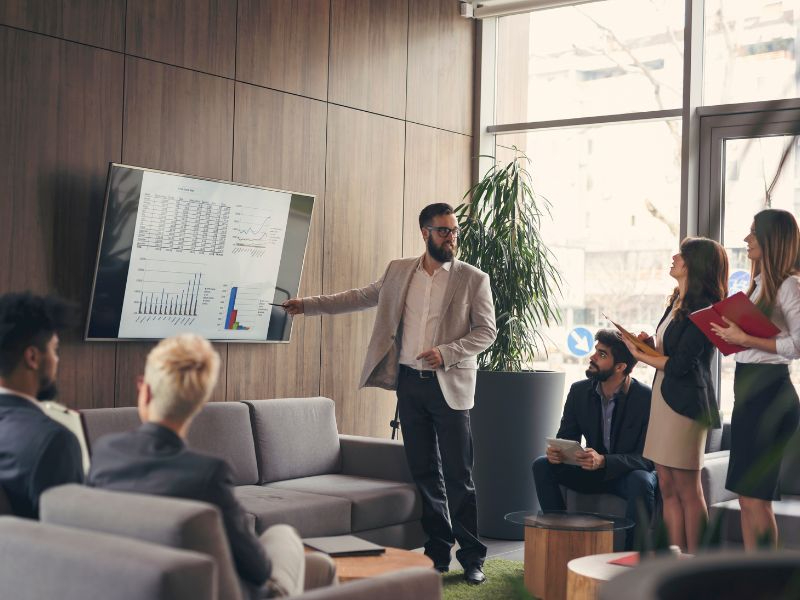