[VIDEO DEMO] Medical test kit packaging machine with integrated robotics
By Scott Miller on December 7, 2020
Automated packaging machines play a vital role in the health care industry, now perhaps more than ever.
In the midst of a global health crisis, safe and efficient packaging of medical supplies, test kits, and pharmaceuticals is essential. A strong manufacturing and packaging supply chain in the medical industry is vital to ensure supplies and test kits reach those who need them most, when they need them most.
I'm Scott Miller, Viking Masek's VP of Product & Technology, and today I'm taking you on a video walkthrough of a complete 8S-235 pouch packing system for medical test kits, including robotics.
STEP 1: Load bags into machine & optional print
Pouches are loaded into a bag magazine which then feeds them into the body of the machine at station 1.
The 8S-235 is designed so a printer can be mounted on station 1. This allows for clear and concise printing of date or lot codes on the pouches prior to them moving through the system.
STEP 2: Quality control via vision inspection & rejection
Quality control is of utmost importance in the medical packaging industry. Many manufacturers of medical test kits and devices opt for vision inspection at multiple times during the packaging process.
On this particular medical test kit packaging system, the first vision inspection station detects the height of the pouch in the grippers as it is loaded into the body of the machine. This allows for proper pouch placement within the grippers within +/- 1-2 mm. If the pouch is not within that range, that means it was not placed within the gripper assembly correctly and will be rejected.
The second vision inspection system is OCR (Optical Character Recognition), which is used to detect the quality of the print that was placed on the pouch at station 1. With an OCR vision inspection system, we can inspect the print to see if it is correct. If it is not, we can reject that pouch.
When a pouch is rejected for any reason, the subsequent stations (bag open, fill, sealing, etc.) will not engage, minimizing product loss and allowing for reuse of the rejected pouch in a future cycle.
STEP 3: Open zippers on premade pouches
If the pouch is fitted with a zipper, this station will open the zipper portion of the pouch using vacuum suction and opening jaws.
STEP 4: Open premade pouches
The bag open station uses vacuum suction cups to grasp and pull open the bag. The detection within the bag opening station allows the machine to see if the bag is actually open. If it is not, subsequent stations will not engage.
STEP 5: Place components into pouches using robotics
On this particular medical test kit packaging system, a pick and place robot grasps and deposits a kit component into the pouch. The robot eliminates the need for manual picking and placing, as some of these packaging processes are rather labor-intensive, precise, and time-consuming. When it comes to robotics, we give our customers a choice of robot manufacturer. Our technicians then integrate the robotics with the packaging machine.
This particular robotic configuration also includes its own flighted infeed conveyor. A human worker would place the components into the flighted conveyor. Alternatively, a different packaging equipment component could automatically feed the conveyor, eliminating the need for human labor at this stage. The choice is largely dependent on client specifications and budget.
STEP 6: Additional quality control via vision inspection & rejection
This vision inspection system detects whether the component placed by the robot into the pouch is in the correct position and all the way inside the pouch. If the component is seen to be sticking up into the seal area of the pouch, the vision inspection system will detect that and will tell the next station to not seal that particular pouch.
STEP 7: Seal & cool premade pouches
This station uses a heated bar to bond the layers of the pouch together creating a strong seal. This is immediately followed by a cooling station that further strengthens the integrity of the seal.
STEP 8: Discharge finished pouches
The finished pouch is now discharged onto the takeaway conveyor and out into the downstream process.
STEP 9: Optional downstream equipment
If the customer desires, an inline checkweigher can be added to the packaging system at this point, which would provide one last quality check as to whether the pouch is filled to the proper weight.
Learn more about packaging equipment for medical test kits
Interested in automating the packaging of single or multi-component medical test kits? Whether your product is related to COVID-19, influenza, antibody presence, or other diagnostics, a custom pouch packaging system can be configured to meet your exact specifications. Learn more at our Medical Test Kit Packaging Hub:
Visit medical test kit packaging hub >>Related Posts
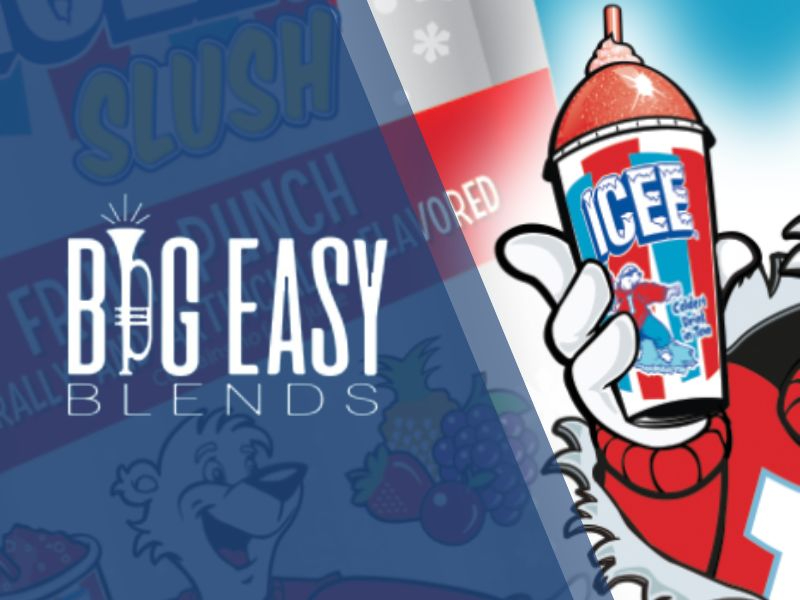
Delivering packaging excellence: How Big Easy Blends improved quality with packaging automation
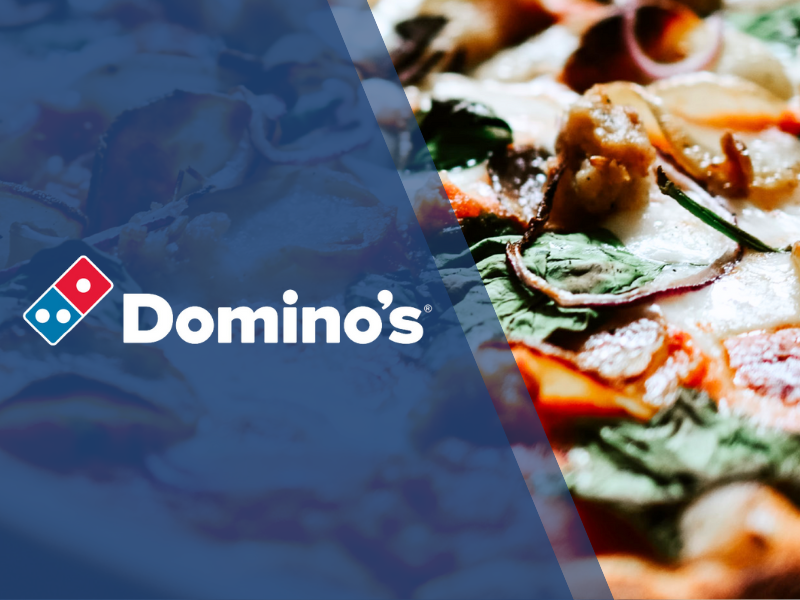
Top this: How Domino’s packages its toppings 60% faster
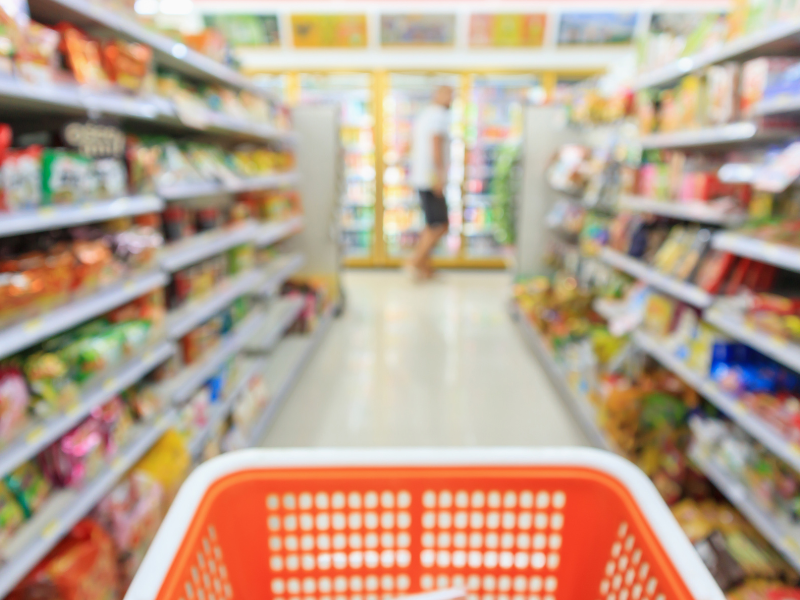