Liquid Packaging Essentials: 3 important details you must know
By Robb Leonhard on February 12, 2021
Whether it's sauces, thick creams, gels, or even water, automated liquid packaging is quick, clean, and easy using modern flexible packaging machines.
If you're looking to automate your liquid pouch packaging, there are three main things your packaging equipment manufacturer or integrator needs to know to provide the best liquid packing machine for your application.
Planning a liquid packaging machine project?
Afraid you're going to miss vital details when spec'ing a new packaging machine? Download our free project planner and rest easy >>
1. Viscosity is the name of the game in liquid packaging
Viscosity is defined as a measure of a fluid's resistance to flow. It describes the internal friction of a moving fluid. In more informal terms, it's a measure of the liquid product's 'thickness'.
A liquid with higher viscosity, such as icing or molasses resists motion because its molecular makeup gives it a lot of internal friction. It doesn't flow as easily. In contrast, a fluid with lower viscosity, such as water or corn oil flows easily because its molecular makeup results in very little friction when it is in motion.
The mathematics required to calculate viscosity is much too involved for a packaging blog and can be most easily measured with special equipment. However, a simplified formula for measuring viscosity is as follows:
viscosity = shear stress / shear rate
or
μ = τ / γ
The answer is usually expressed in centipoise (cps). Water is the standard at 1 cps. A liquid product like honey would have a viscosity of about 10,000 cps. Condiments like ketchup or mustard have a viscosity of 50,000 - 70,000 cps.
So what does viscosity have to do with packaging, anyway?
CSC Scientific Company Inc., a provider of measuring equipment, explains that in the Consumer Packaged Goods (CPG) world, viscosity affects the rate at which a liquid product travels through a pipe, how long it takes to set or dry, and the time it takes to dispense the fluid into its packaging.
When it comes to selecting liquid packing machines, the viscosity of the product is a vital detail and must be accurate. Viscosity determines the type of product filler used: It must provide the right amount of force to induce flow, but not so much that the packaging will overfill.
2. Fill temperatures affect viscosity of liquids
When heated, most liquid products flow more readily. Picture the consistency of frosting or motor oil as it is heated; its viscosity lowers significantly and it becomes much more free-flowing.
Here's what's happening: When a liquid is heated, its molecules begin to move faster and faster. This movement is enough to overpower the forces that bind the molecules together, resulting in a more free-flowing liquid. Heat also causes a decrease in surface tension, further reducing viscosity.
How does this affect the packaging process?
The temperature at which the liquid product will be filled into the package is very important to the configuration of the packaging line, specifically when it comes to the product filler.
To provide the most efficient liquid packaging solution, providing an accurate fill temperature is a must. Inaccuracies in this area can result in packaging equipment that isn't specified for your needs, causing malfunctions and frustration.
3. Size matters when it comes to particulates
Liquids like salad dressings, soups, and sauces often contain particulates. These particulates are usually spices and flavor additions like small vegetable pieces. Particulates can be suspended in the liquid product or they can settle toward the bottom of the fluid.
When packaging liquids with particulates, special care must be taken to accurately describe and measure their average size and general properties.
The presence of particulates will determine the type of product filler your liquid packaging solution will require for the most accurate and unimpeded dispensing.
Automated liquid packaging solutions
As a leading liquid packaging machine manufacturer, Viking Masek has installed a variety of packaging equipment in facilities for liquid packaging projects like:
- Airless hot fill bulk soups with particulates on liquid form fill and seal machines
- A variety of liquid products filled into new premade STANDCAP pouches
- Filling and sealing sauces into premade stand-up pouches
- Liquid and gel cold packs for meal kits and medical/therapeutic use
- Small single-serve sticks of condiments, flavor enhancers, and boozy freeze pops
Visit our liquid packaging machine hub to learn more about the different types of equipment used for packaging fluid products.
Download a liquid packing machine project worksheet
Make sure your next liquid packing machine is manufactured to meet your exact needs, including things like viscosity, fill temperatures, and particulate properties. Download a free planner that will help you define over 50 key details vital to the success of your equipment acquisition:
Get your FREE project planner >>
Originally published 8/31/2016, updated 6/5/2018, 2/12/2021.
Related Posts
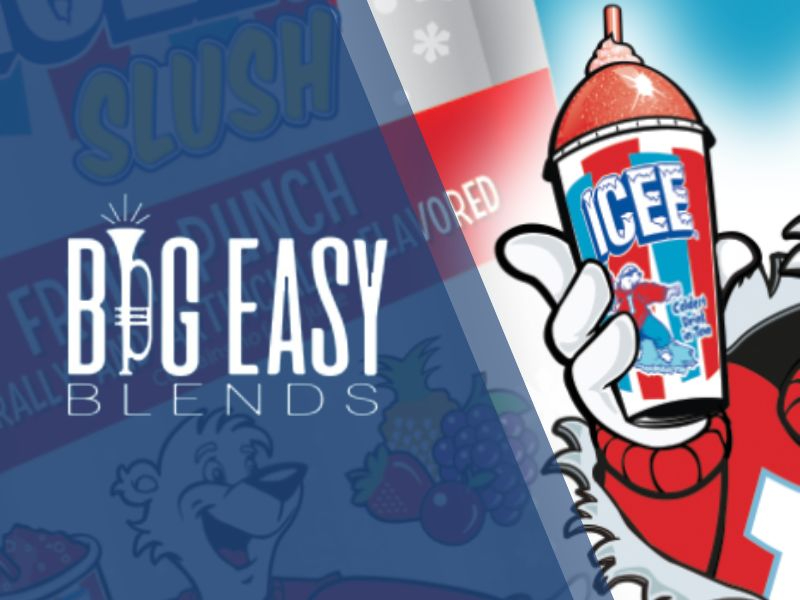
Delivering packaging excellence: How Big Easy Blends improved quality with packaging automation
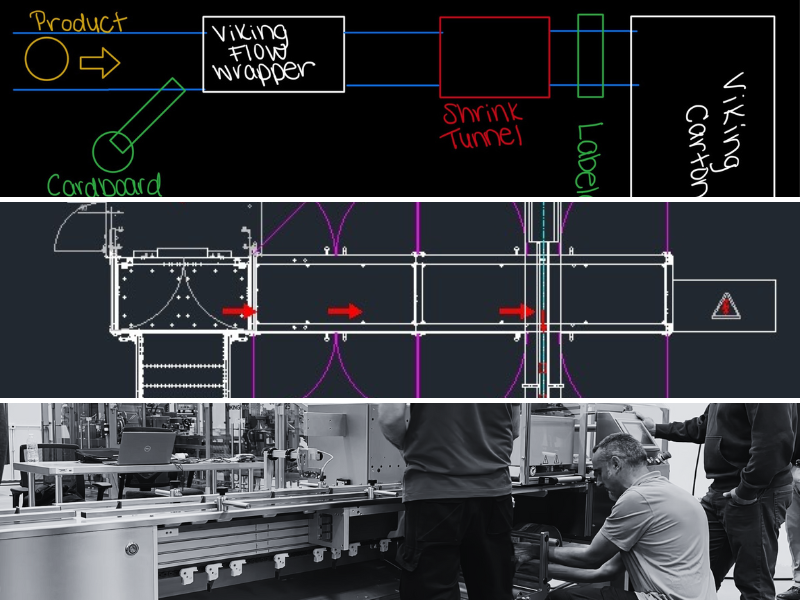
Optimizing packaging efficiency: The role of Flow Wrapping Machines in integrated systems
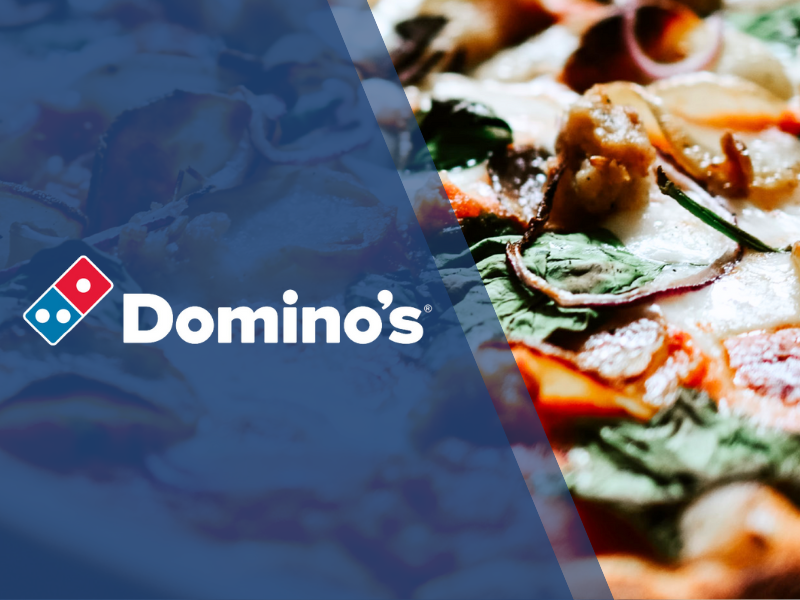