Troubleshooting 10 common VFFS packaging machine issues
By Scott Miller on August 6, 2019
It's not fun when your VFFS packaging machine throws an error code.
But with proper preventive maintenance and training, vertical form fill seal troubleshooting should be infrequent and easy.
Need help troubleshooting your Viking machine? Contact support here >>
General vertical form fill seal troubleshooting
Error messages report issues with the VFFS machine. Every trouble report will stay displayed on the HMI screen until it is acknowledged by an operator.
Before getting into the specifics of your issue, ask yourself 3 general questions:
- Is the machine set up in the correct environment as specified?
- Are the ambient temperature and humidity levels as specified?
- Are there any other factors that may cause potential issues with the machine, product, or film?
If the environment, temperature, or humidity levels in your facility deviate from what your vertical form fill machine was specified for, this can cause malfunctions. Additionally, if you have recently changed the machine over to an untested new product or film, it may need some tweaking. If the above questions don't uncover anything abnormal, you can move on to more specific VFFS troubleshooting, starting with 10 common issues and their possible causes below:
NOTE: These are general tips. Your machine may not have all features listed. Consult your owner's manual or machine manufacturer's service department for VFFS troubleshooting specific to your machine.
1. The machine does not power up
Possible causes:
- Incoming power issue
- Main disconnect is off
2. The machine does not reset
Possible causes:
- Safety circuit not reset
- Low air pressure
- Guard doors open
- E-Stop
- Faulty wiring
- Bad safety relay
3. Low air pressure
Possible causes:
- Machine not reset
- Safety circuit not reset
- Incoming air pressure low
- Low air pressure during run mode
- Supply airline too small
4. The temperature of the jaw is out of range
This means the set jaw temperature does not correspond to real temperature. In this situation, you should check all wiring and connections using electrical prints. Also verify the solid-state relay light is coming on.
Possible causes:
- Sealing jaws are not warmed up
- PLC fault
- Temperature sensor fault
- Heater fault
- Faulty fuses or breakers
5. Jaws are not working
This error means the jaws cannot completely open.
Possible causes:
- Assembly not able to function freely
- Low air pressure
- Air cylinder fault
- Cylinder slide fault
- Piston position sensor fault
- Air distribution fault
- E-Stop during machine run
6. Printer does not work
Possible causes:
- Printer is not ready to run
- Printer is switched off
- Printer cable is damaged or disconnected
- Printer ribbon is broken
- Printer is damaged
7. Film is not tracking properly
This means the film is not moving through the machine properly. First, check to make sure the film carriage moves freely. Also check all wiring, relays, and power to the motor. Wipe the film brake roller clean.
Possible causes:
- Film is not centered on spindle
- Film is not webbed up properly
- Rollers and dancer levels are parallel
- Film is loose on one side and tight on the other
- Splice table clamps down
- Rollers not spinning freely
- Auto film tracking not working
- Forming tube damaged or not installed properly
- Splice tape stuck in forming tube
- Pull belts not set up properly
- Brake roller dirty
8. Bad vertical seals
This error means the vertical seals on the packages are inadequate. First check the film tracking to make sure film is properly loaded, folded, and in position. Work with time, temperature, and pressure settings to create acceptable seals. Also check the foam and tape on the forming tube.
Possible causes:
- Forming tube backstop set improperly
- Incorrect distance between film and forming tube
9. Bad cross (horizontal) seals
This error means the horizontal seals on the packages are inadequate. First check to make sure the jaws are properly aligned and that there are no wrinkles on the film. Work with time, temperature, and pressure settings to create acceptable seals.
Possible cause:
- Product in end seal
10. Jaw jam
This means there is something causing a jam in the sealing jaws.
Possible causes:
- Product in end seal
- Incorrect timing between filler and bagger
- Jaws not set up properly
- Jaw air pressure low
VFFS troubleshooting and maintenance
With a proper preventive maintenance plan, vertical form fill seal troubleshooting should be infrequent and easy. Need help getting started? Download our free VFFS Preventive Maintenance Planner:
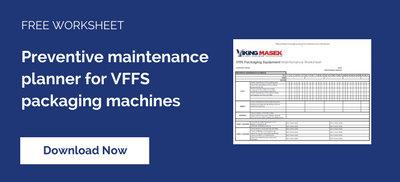
Have a bigger issue and need to talk with a certified Viking technician about your VFFS packing machine? Contact us today.
Related Posts
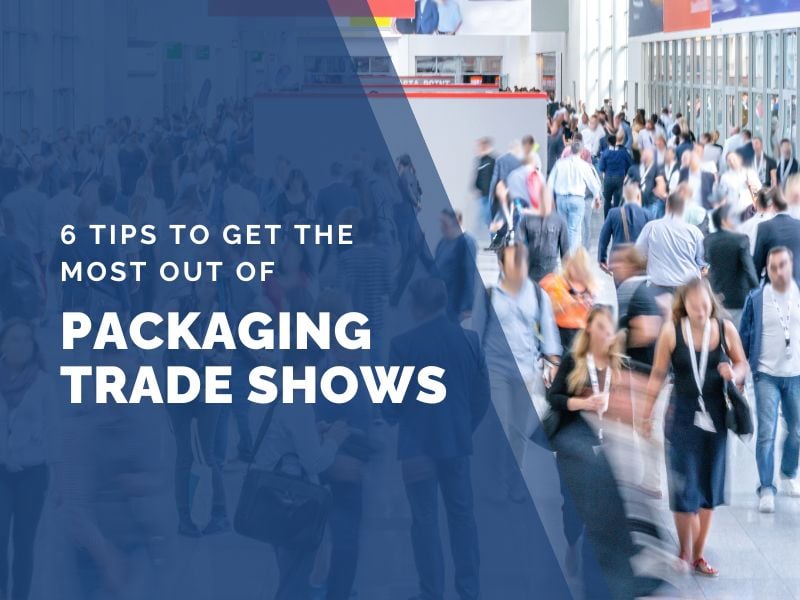
Discover Top Tips for Shopping Packaging Equipment at Trade Shows | Viking Masek Blog
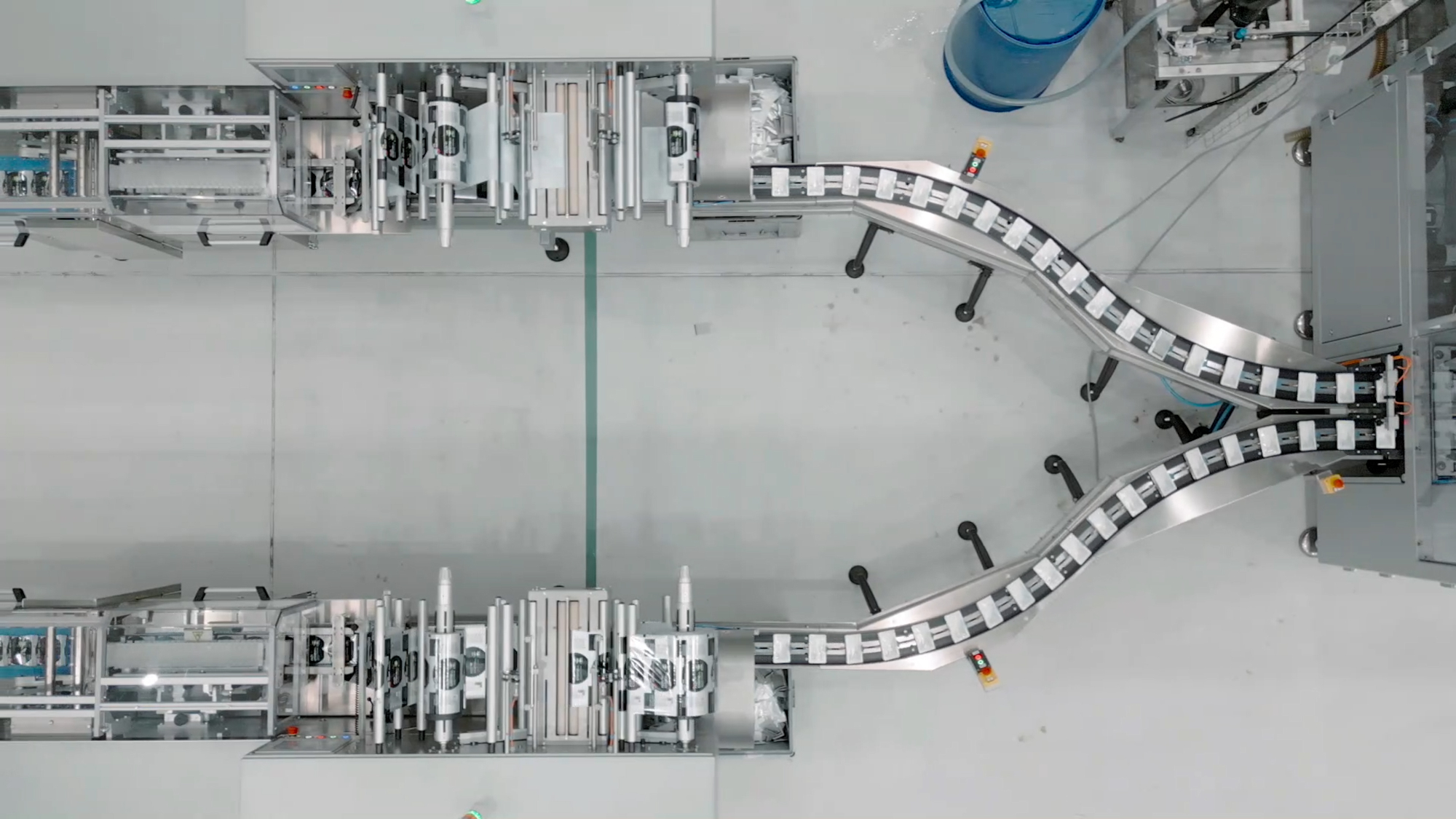
Introducing Viking Masek's advanced flow wrapping equipment
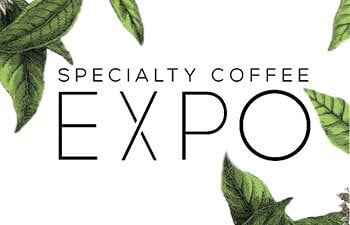