[VIDEO DEMO] How a liquid VFFS packaging machine works
By Scott Miller on February 17, 2021
Companies that package liquid products often want two things in their automated packing system: A clean packaging process and the ability to wash down their equipment.
Luckily, modern packaging automation technologies fulfill those liquid packaging requirements...plus much more.
I'm Scott Miller, Viking Masek's VP of Product & Technology, and today I am taking you on a walkthrough of our most unique liquid packaging machine: The VFFS Liquid Sigma.
Intro to the Liquid Sigma VFFS machine
The Liquid Sigma is a continuous motion VFFS machine, meaning the packaging film moves continuously without stopping to receive its vertical seal. This result is faster packaging speeds.
Design
The design of the Liquid Sigma is stainless steel, IP66 washdown. This IP Rating means the machine's enclosures are dust-tight and can be safely cleaned with strong jets of water. The only exception to this design is the jaw carriers, constructed from aluminum for proper weight distribution (stainless steel is too heavy).
Controls
The control system for the machine is an Allen Bradley Panel View 1500 coupled to a Compac Logix PLC and Kinetics 5500 servo drives.
Electrical components
Usually mounted directly to the side of the machine, the electrical cabinet is instead remote mounted on the Liquid Sigma. It can be mounted in a different location, out of the way of the washdown environment. One hundred feet of cable attach the remote cabinet to the machine which allows for flexibility of placement. Two junction boxes on the machine where the cabinet would have been mounted act as the termination points for all electrical components.
With the intro out of the way, let's dive right into our walkthrough, starting at the top of the machine:
1. Liquid hopper & filler
A VFFS liquid packaging process usually begins with the liquid product in a hopper. This hopper can be heated if the product must be packaged at a higher temperature to reduce its viscosity.
A liquid piston pump will draw the liquid product to the top of the machine where a lance will deposit discrete volumes of product into the bag through the hollow center of the forming tube.
2. Bag forming
A wide, flat roll of film is threaded over various rollers through the machine and then threaded over a forming tube assembly which brings the vertical sides of the bag together to begin forming its shape.
The film is transported through the machine by vacuum pull belts. These belts use vacuum suction to grip the film and transport it through the body of the machine.
Vacuum pull belts come as standard on the Liquid Sigma. The advantages of vacuum pull belts include less wear and the fact that the film will not be squeezed tightly against the forming tube and instead will have a 1mm gap. This minimizes film bunching or slipping issues that may arise when using regular friction pull belts.
3. Vertical seal
The Liquid Sigma uses a continuously moving heated band-type vertical seal assembly. This allows for uninterrupted seal creation on continuous motion machines. The band seal does not come in direct, constant contact with the film. Rather, it is set to a fixed gap so it does not squeeze the film against the heated block of the seal assembly.
As the film passes by the heated block in the vertical seal assembly, it bonds the layers of film together to create a strong vertical bag seal.
4. Filling of bags with liquid product
Using a lance that transports the liquid product through the hollow center of the forming tube, the liquid product is deposited into the bag in discrete volumes.
The Liquid Sigma shown in the video above is custom-designed with special components that detect the volume or the fill heights of the liquid in the forming tube itself. As the film moves in a continuous motion, the liquid level within the forming tube area goes from the top sensor to the bottom sensor and stays within that range as the bags are filling.
Typically the bags fill in 1/2 gallon or 1 gallon fills, usually hot fills. However, we have done projects with product temperatures as low as 34° F and as high as 195° F.
5. Squeeze roll assembly
The squeeze roll assembly is designed to provide an airless fill. This means each bag will have zero residual air inside it after sealing.
The squeeze roll assembly opens and closes with every cycle while the film moves continuously. The squeeze rollers are programmed to 'know' that they must close at a specific time in order to provide the pre-specified volume of liquid into the bag.
The design premise behind the squeeze rollers is influenced by the durometer of the squeeze roll material. It is available in a couple of different durometers that are directly related to the desired product fill, the product, and how hard or soft the rollers must be.
6. Cross seal
A set of heated jaws come together to bond the layers of film together to create a strong horizontal seal. The seal of the bottom of the bag and the top of the next bag are created at the same time.
The jaw design on the Liquid Sigma is unique, configured in such a way that it can seal through any residual liquid that is left on the inside of the film. This means each bag will receive a strong seal and you won't have to worry about messy, leaky bags.
7. Bag discharge
At this point, the finished bag is cut and discharged from the machine. It can either be deposited into a receptacle or dropped directly onto a conveyor to transport it to downstream equipment like checkweighers, carton packing, or case packing.
Additional Liquid Sigma Features
Film carriage
The film carriage on the Liquid Sigma is 100% stainless steel, allowing for 100% washdown. In most cases, customers are cleaning with caustic cleaning foam and rinsing with a hot rinse. Stainless steel construction means you can aggressively wash down those components and not have corrosion issues or breakdown of metals.
Powered film unwind
The film unwind has a surface assist. Films for liquid products tend to be a little more slippery and the surface assist provides a positive unwind and helps the film move through the system easily.
Extra film spindle
Many clients opt to purchase an extra film spindle so they can have an additional roll ready when it comes time to change rolls. This saves time during splice cycles.
Film splice table
Above the roll of film, you will see a splice table, which is used to join the end of a spent roll of film to a new roll. This will automatically draw the new roll of film through the machine without having to manually re-thread it.
Printer
Clients can opt to add a printer to their Liquid Sigma for date coding purposes. Located directly in the film path, the printer is usually not fully washdown, so care should be taken to remove or protect it during washing cycles. Enclosures are available to protect key printer components during washing.
Guide for first-time liquid packaging machine buyers
Don't know what to look for when shopping for a liquid packing machine to make sure you get the right equipment for your business? Download our free buyer's guide to learn all you need to know to make the most informed decision.
Related Posts
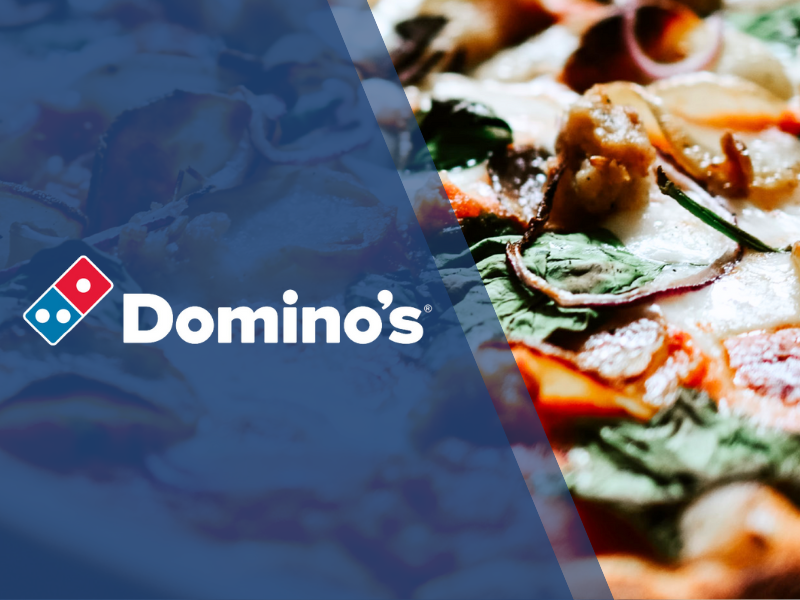
Top this: How Domino’s packages its toppings 60% faster
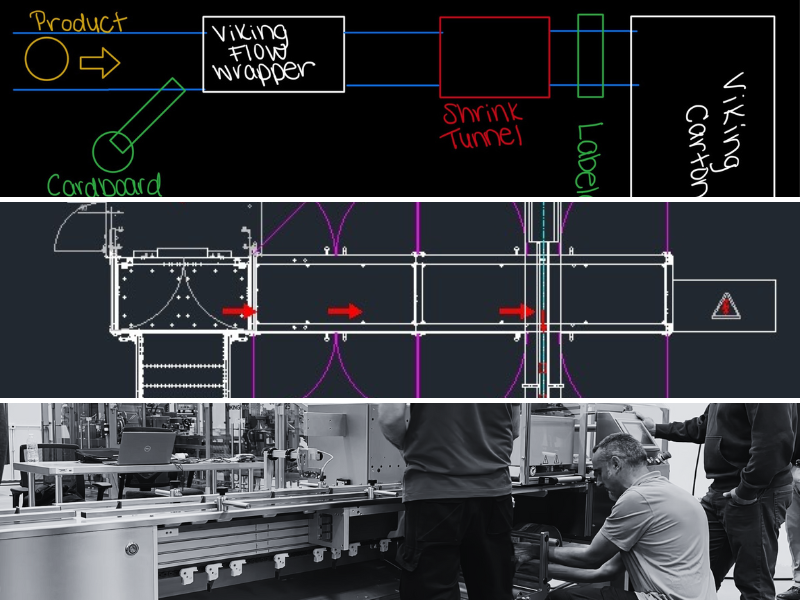
Optimizing packaging efficiency: The role of Flow Wrapping Machines in integrated systems
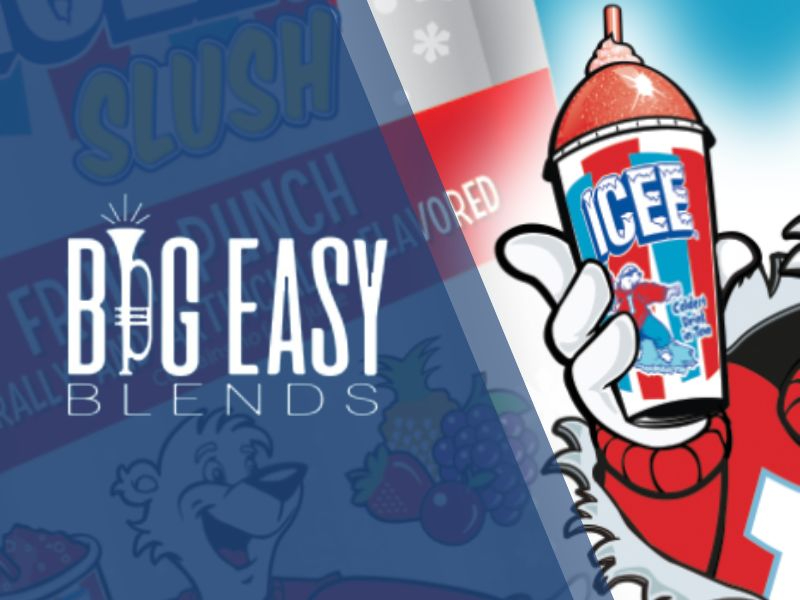