How High Speed Twin VFFS Velocity Can Transform Your Packaging Process | Contract Packaging | Coffee Packaging
By Scott Miller on July 15, 2019
If you’re a coffee roaster or co-packer, your wishlist for coffee packaging machinery likely focuses on the trifecta of speed, accuracy, and performance.
We hear you! So after collaborating with industry leaders, we made some advances in our high-speed coffee packaging equipment, improving the process from start to finish. The result: A newly upgraded continuous motion Twin VFFS Velocity.
Here are 4 ways this innovative system can transform your coffee packaging operations:
1. Unmatched speeds
The Twin VFFS Velocity can reach true production speeds of up to 350 bags per minute (175 bpm per side).
The vertical form fill seal Velocity is the fastest VFFS machine in the world, period. Why? Standard VFFS machines have a single sealing jaw, whereas the Velocity features two patented, independently-phased, continuous motion sealing jaws.
With two jaws at work in tandem, lost cycle time is virtually eliminated which allows for tremendous increases in coffee packaging speeds. The Twin Velocity doubles these already high speeds, featuring two lightning-fast machines side-by-side. By the numbers, the Twin VFFS Velocity can reach true production speeds of up to 350 bags per minute (175 bpm per side).
2. Improved technologies
Machine controls
The Twin Velocity is fully servo, featuring the latest Allen Bradley technology. This means superior control over bag length, sealing, and web handling which allows CPG companies to reach higher speeds while still producing high-quality coffee packages. The controls also feature as standard (at no extra cost to the customer) built-in Ethernet connectivity. This makes remote troubleshooting even more convenient and cost-effective for the user.
Back seal design
An improved fully servo back seal design self-centers and ensures a consistent vertical seal quality. The sealing assembly now floats to better conform to the smaller forming tubes used for fractional packs of coffee. If you have strict back seal width requirements, this improved design will meet them.
Full integration and automation
Controls for both the bagger and auger filler are integrated into the packaging machine’s PLC (programmable logic controller) and are all accessible through the one touchscreen HMI (human machine interface) on the VFFS Twin Velocity. This gives operators full control over the system from a single point, making setup and operation of a dual system easier.
3. High accuracy
Package weights
During testing, only 75 bags out of 10,000 were outside of acceptable weight parameters, for 0.8% give away.
Achieving package weights within specified parameters is very important for CPG companies. In a recent test using ground coffee, the Twin Velocity system dosed to accuracies of +/- .01 ounces on a small 2.5-ounce fractional package. During this same test, only 75 bags out of 10,000 were outside of acceptable parameters, for 0.8% give away.
Seal integrity
On the Twin Velocity system, the auger dosing equipment features superior product control, so no particulates end up in the cross seal, even at high speeds. This means strong package seams and fresh, quality coffee for your end consumers.
4. Sustained cost savings
Labor reduction
With the Twin Velocity coffee packaging solution, one operator can effectively run two systems. This means double the output with half the labor requirements right off the bat.
But wait, there's more! The integrated and fully automated real-time check weighing system eliminates the need for human inspection and intervention. If a bag is out of spec, a rejection arm pushes it off the line, and that data is communicated immediately to the PLC and changes are made to dosing on the fly.
But that's not all! Further down the line, cases are erected, a high-speed counting head counts filled bags of coffee, fills the cases with a predetermined amount of packages, and closes the boxes. Again, all without the need for human intervention. Needless to say, the long-term cost savings from elimination of manual labor alone make this system a smart investment.
Waste reduction
During a manual inspection process, a laborer has to pull a set number of bags off the line at predetermined intervals to inspect them for quality and weight compliance. If packages are found to be out of spec, the entire run may have to be scrapped and redone.
With the closed-loop check weighing process on the Twin VFFS Velocity system, dosing adjustments are made automatically, in real-time, pouch-for-pouch. This results in a dramatic reduction in product give away and substantial long-term cost savings via decreased product waste.
Take your coffee packaging to new heights
Interested in the possibilities of advanced high-speed coffee packaging automation? First, assess your current packaging process to see where you could improve. Use our free comprehensive Coffee Production Planning Spreadsheet to evaluate your current setup and see how packaging automation can help:

Originally published 2/22/18, updated 7/15/19.
Related Posts
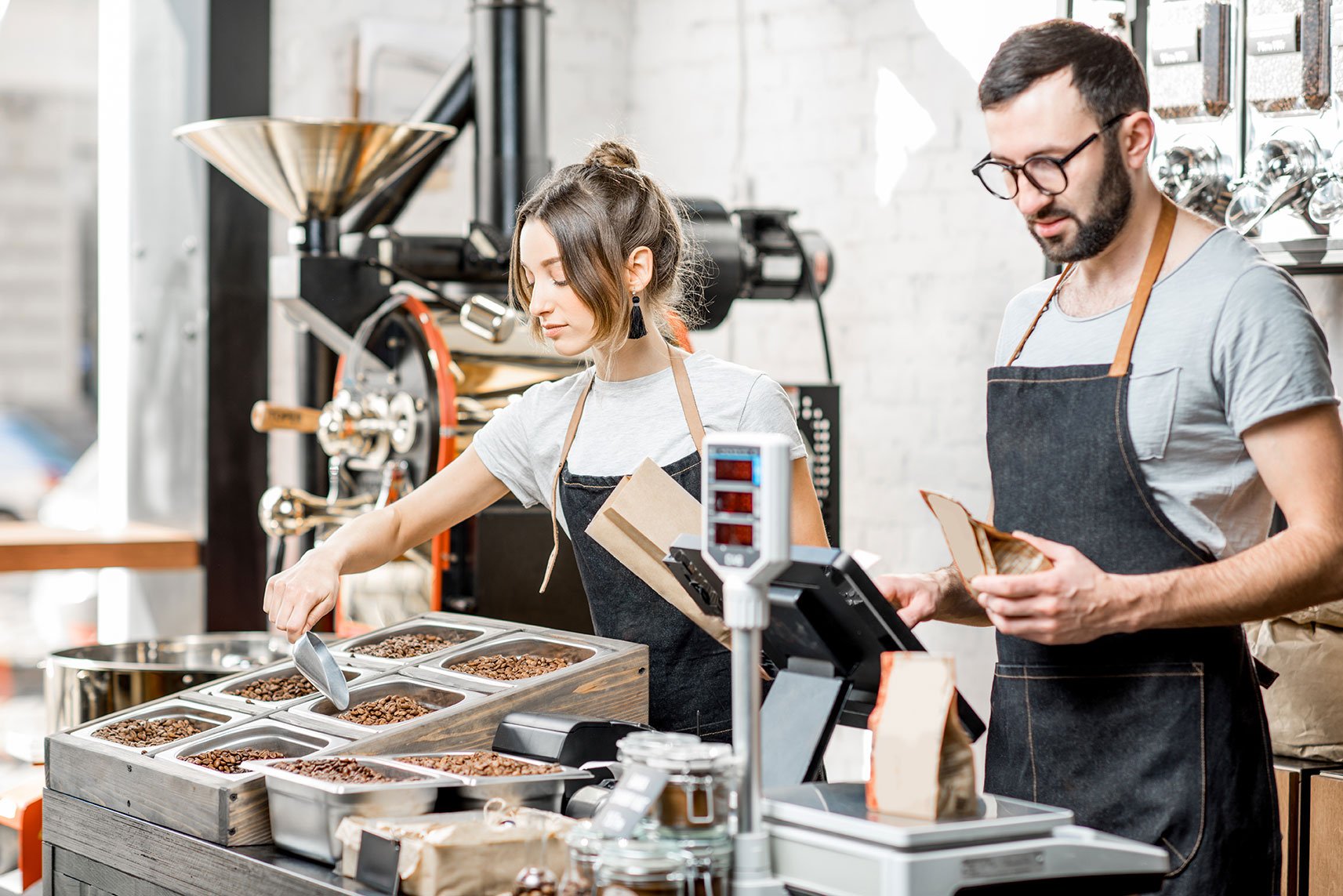
Packaging Your Morning Pick-Me-Up
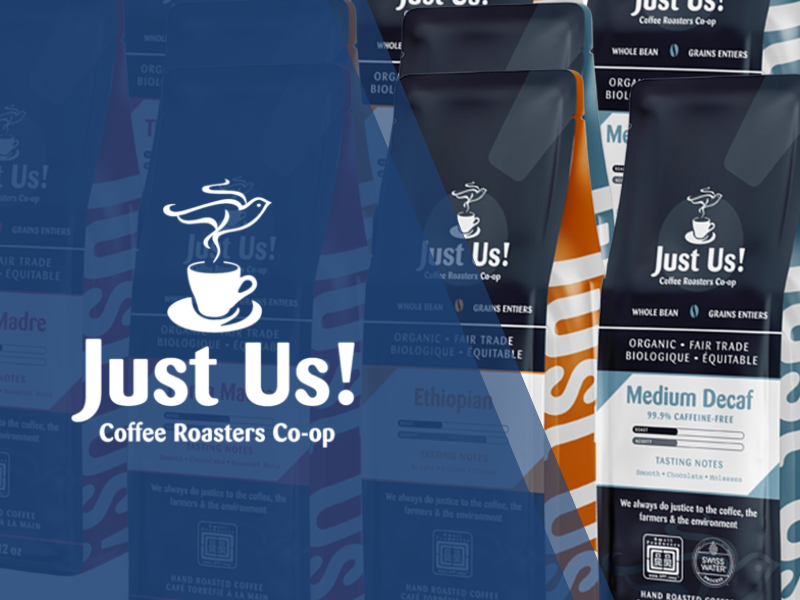
Brewing success: How Just Us Coffee automated coffee packaging to perfection
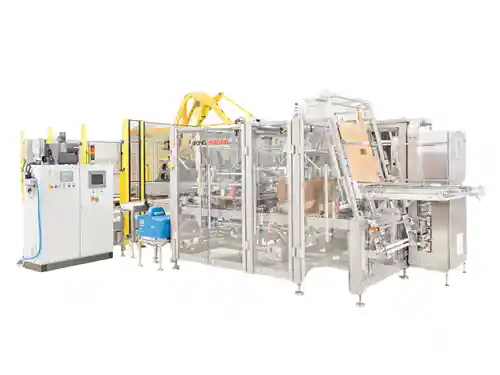