Meet the 4SC-235: Our most compact, user-friendly pouch packing machine yet
By Danielle Ohl on January 28, 2022
Viking Masek had a vision: A user-friendly, streamlined, compact pouch packing machine at an affordable price point.
The issue was, it didn't exist yet. So our team went to work.
Ten months and over 2,000 person-hours later, we're officially announcing the release of our new premade pouch machine model 4SC-235.
Our most simplified, compact pouch packing machine yet, the 4SC-235 packs high tech into a small package.
Great for small businesses and those new to packaging automation, the 4SC-235 is 100% made at our US headquarters in Wisconsin.
The story behind the machine
The journey began when Viking customers began requesting a compact, affordable premade pouch machine with lower throughput. Many smaller clients desired equipment made in the USA using Viking smart technology, but did not need high-capacity equipment and couldn’t justify making a substantial investment in a comprehensive packaging system right off the bat.
"Our team is always looking for ways to help our customers do business better, no matter what stage of business development they are in," comments Bryan Lacy, Viking Masek Director of Sales. "We recognized that our product lineup largely catered to clients who require maximum throughput and custom packaging solutions. After listening to our customers’ challenges, our team saw a gap in the market for a more affordable, user-friendly pouch packaging option to meet the needs of quickly growing small businesses and niche markets."
[Viking Masek's] team saw a gap in the market for a more affordable, user-friendly pouch packaging option to meet the needs of quickly growing small businesses and niche markets. - Bryan Lacy, Director of Sales
To officially kick off the project, a cross-functional Research & Development group met internally, and an initial concept was developed by Viking’s in-house engineers. Knowing that affordable linear models were already available on the market and that a rotary design was more compact and ergonomic, the team decided they wanted to focus on bringing an affordable, common sense, rotary model to market.
"The development of the 4SC pre-made pouch machine allows Viking to help an entirely new customer market," explains Robb Leonhard, Viking Masek President. "It also gives our existing brand loyal customers a compact, highly productive, premade pouch packaging solution."
The development of the 4SC-235 allows Viking to help an entirely new customer market. It also gives our existing brand loyal customers a compact, highly productive, premade pouch packaging solution. - Robb Leonhard, President
After the initial concept and design were created, customer-facing teams were consulted to provide input about specifications that would match the needs of our clients. Weekly design meetings with the team ensured ample opportunity for feedback and revisions, leading to several iterations before the team finalized a comprehensive design.
"We’ve developed a very robust R&D team that has well beyond the technical capabilities, is 100% committed to their craft, and solely focuses on market desires brought by raw feedback supplied from our customers and customer-facing teams," comments Ty Weinhold, Viking Masek COO.
We’ve developed a very robust R&D team that has well beyond the technical capabilities, is 100% committed to their craft, and solely focuses on market desires brought by raw feedback supplied from our customers and customer-facing teams. - Ty Weinhold, COO
An exciting component of the project was utilizing Viking's 3-D printer, enabling more efficient testing as team members could print new components in hours instead of waiting days to weeks for parts to be fabricated and shipped.
"It was an exciting challenge for the entire team to develop this machine from the ground up," comments Mike Schaap, R&D Manager for the development of the 4SC-235. "From numerous design review meetings to completing designs to longevity testing, and finally to a working machine and gathering team input and enhancement changes, we have a new machine platform that will exceed our customer’s needs."
From numerous design review meetings to completing designs to longevity testing, and finally to a working machine and gathering team input and enhancement changes, we have a new machine platform that will exceed our customer’s needs. - Mike Schaap, R&D Manager
What sets the 4SC-235 apart
The R&D team focused on not only creating a more affordable machine without sacrificing build quality, but their goal was also to innovate and develop technologies that truly provide a measurable value to clients.
"With these new innovations, we can now help clients automate costly manual packaging processes earlier in the game, putting them on the path to long-term success without sacrificing the premium build quality that’s often seen in entry-level equipment offerings," says Lacy.
stress-tested Bag grippers
A major initial design focus of the 4SC-235 project was the bag grippers. Knowing they get a ton of use, their integrity and longevity were crucial. So crucial, in fact, that final testing included running the assembly through 1.5 million cycles!
Combined functions to decrease space
Next, the team devised a way to combine multiple machine functions into a single assembly, allowing for a more compact design and decreased material cost, with those savings passed on to the end customer.
streamlined infeed
The infeed was also an area of focus. Other pouch packing machine models require an attentive and trained operator to 'shingle' the pouches correctly as they feed into the machine. Desiring a more user-friendly, hands-off option, a stacked infeed was designed that allows an operator to easily load up to 1000+ bags at a time, and then walk away until the magazine needs to be refilled. This means minimal training is needed to load the machine with bags, plus the operator is free to spend time on value-added activities.
Simple changeover
Featuring visual scales and measurements, machine adjustments are easily completed and repeated without tools or a high level of technical knowledge, making it easier for casual operators to run the machine successfully. Also featuring manual bag width, length, and height adjustments, changeover to different size bags is quick, simple, and requires minimal skill. Visual indicators also reduce operator training issues due to language barriers.
simplified interface
To make the machine even more user-friendly, the HMI (human machine interface) has been programmed from scratch to be greatly simplified. Opting for a cleaner interface makes operator training a cinch and reduces room for error.
very minimal maintenance
Most equipment manufacturers can say their equipment requires minimal maintenance, but with the simplification in design and streamlined workflow of the 4SC-235, Viking really means very minimal maintenance. Ultimately, when wear parts do need replacing, they can be 3-D printed at Viking's US headquarters or sourced locally, meaning lead time for replacement parts will be greatly reduced.
What's next on the horizon
Many of the discoveries and innovations realized because of this project can also be applied to Viking's existing product portfolio to continuously improve their value to end-users.
"The industry is in desperate need of automated manufacturing technologies that have the intelligence to adjust, size change, troubleshoot, and run themselves without the need for operators," comments Scott Miller, Viking Masek VP of Business Development. "We expect to lead the industry as we develop new high-speed VFFS and premade pouch machines, coupling them with new high-speed automated secondary packaging. All of this will be done with the customer in mind, with the goal of reducing the manual labor needed to meet or exceed current demands."
We expect to lead the industry as we develop new high-speed VFFS and premade pouch machines, coupling them with new high-speed automated secondary packaging. All of this will be done with the customer in mind, with the goal of reducing the manual labor needed to meet or exceed current demands. - Scott Miller, VP of Business Development
Learn how the 4SC-235 can transform your growing business
Want to learn more about the 4SC-235 pouch packing machine? Click through for in-depth technical specifications, pictures, machine options, and more:
Get the details >>
Viking Masek in the news:
Cannabiz Media - New automated pouch packaging machine set to transform operations for small businesses
Cannabis Business Executive - New automated pouch packaging machine set to transform operations for small businesses
NS Packaging - Viking Masek rolls out new automated pouch packaging for small business
Related Posts
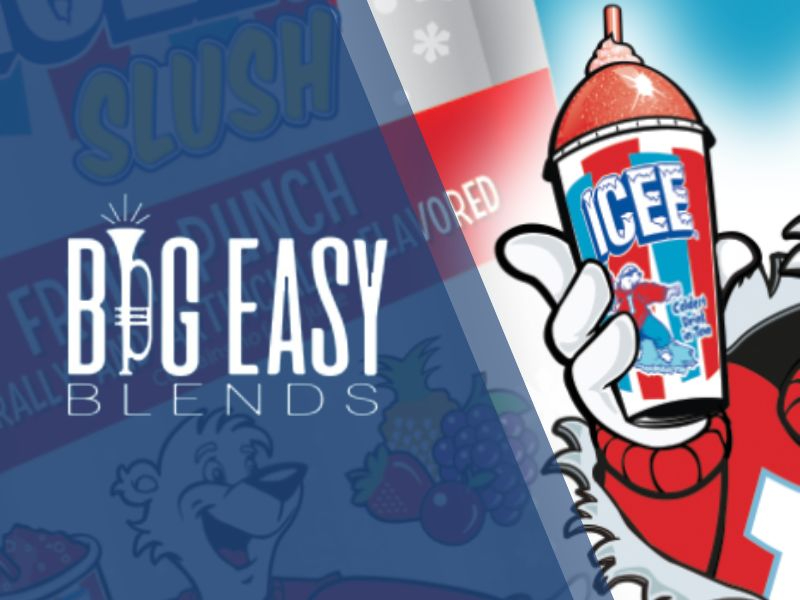
Delivering packaging excellence: How Big Easy Blends improved quality with packaging automation
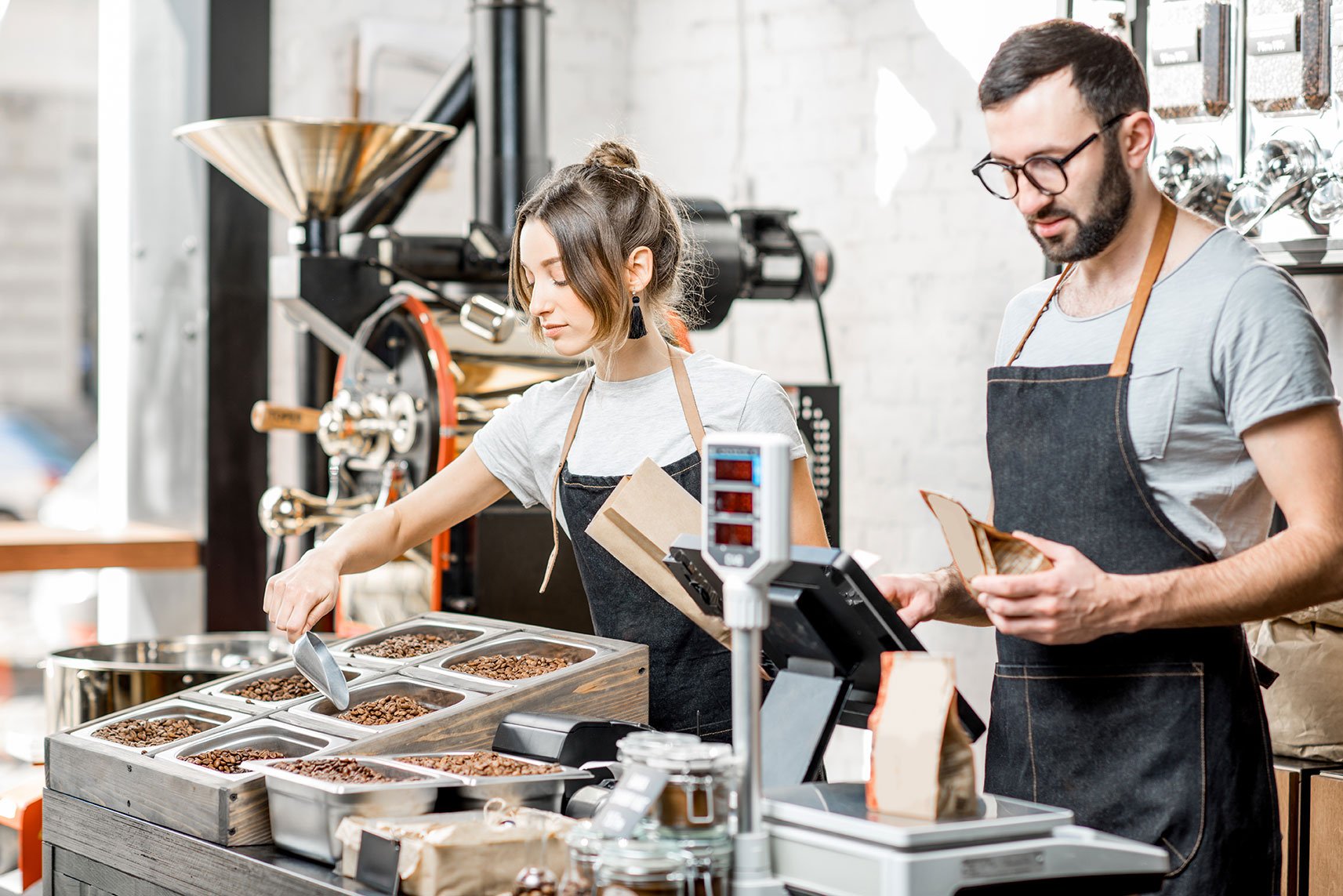
Packaging Your Morning Pick-Me-Up
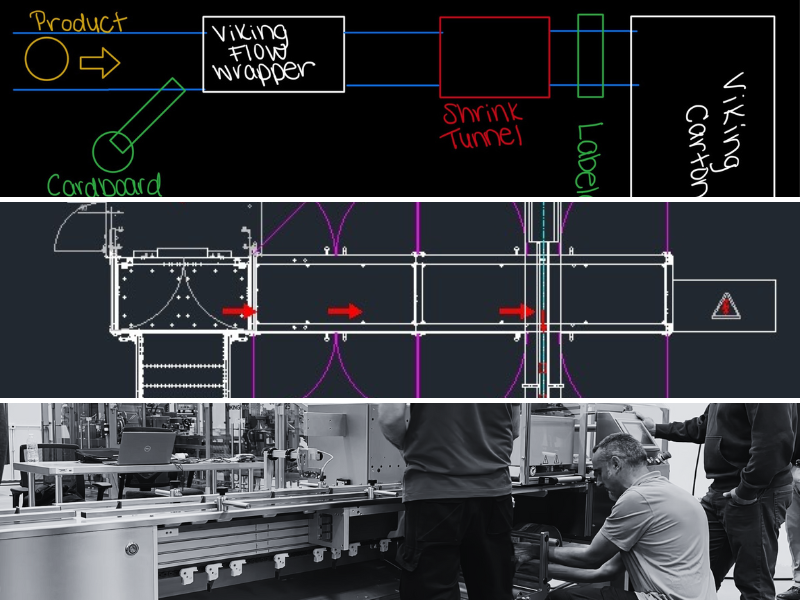